
→As a result, more advanced analysis such as motion analysis including friction, interference check with dimensional tolerances,Īnd motion analysis of play by clearance will be realized. →This will realize the future disused of 2D-CAD. Only the required numbers are registered and the default is not entered. : Perform standardization at kernel level. (3)Profiles of surface dimensional tolerance, geometric tolerance, surface roughness, coefficient of friction, notes,etc. Calculation load is heavy and error-prone contact constraint calculation is reduced.Ĭontact constraint is used only in limited cases such as motion confirmation by gear clearance) (Right-and-left synchronization, Move in order ,thread pitch, etc.

(2)Advancement of motion constraints and standardization at the kernel level.
#Me10 cad manuals
・Interpreter, BASIC like, 1 Drawing (action) 1 command, Manuals are in place,Įcho function (command history), trace function (command + variable history),Įxternal command (OS command, BAT, EXE) remote execution function (variable and result via files), etc. My hope is high level language of me10 macro language level It is impossible for machine design engineers to customize using C language or Python.
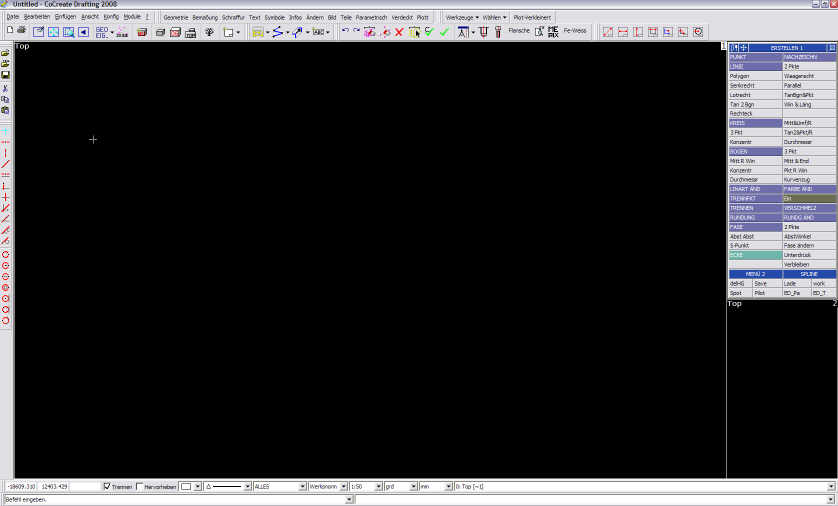
(1)Prepare a macro language that machine design engineers can use. 3.Ideal standard of mechanical 3D-CAD 10 years from now ①In the 3D-CAD motion analysis at the present time, the friction is 0, and no analysis considering the friction in the real world has been made. (6)What can not be done with current 3D CAD analysis There is no such information in 3D-CAD at present, and there is no standardization even if there is a part. ①Parts production at this time except for 3D printer production and mold digging part processing, a large process (casting, welding structure, press production, etc.) is decided by 2D drawing information, and each process worker makes it while looking at dimensional tolerances, geometric tolerances, surface roughness, and other notes of faces described in 2D drawings. (5)Reasons why 2D-CAD is not lost at present and can not be completely transferred to 3D-CAD. ①Joint constraints are not attached to commercially available 3D-CAD data, joint constraint setting is required each time Joint restraint setting because there is no joint restraint Clearance dimension check at that time)Įxample: Take in Kakuta toggle clamp 3D-CAD data from Osaka kakuta Kogyo Co., Ltd. (Operation position specification to check. ①It is necessary to repeat the same operation many times in confirmation after changing link dimensions. ・I changed link dimensions in sketch editing ,and repeated motion analysis then confirmed collision avoidance. ※Because it was not possible to motion order control by synchronization pin, it corresponds by motion study setting. ※Because it was not possible to synchronize the left and right by the rack and pinion, it was substituted by the virtual slide joint. (3)Confirmation of operation of link mechanism and link dimension change simulation ②Joint constraints with low internal calculation load do not have move in order function. With B1 and B2 linked to P, move to the right together. P moves upward with the taper of C (Countersink) of S. (2)Confirmation of operation of synchronization pinĮxplanation of operation of synchronization pin (see the figure below)ī2 (boss 2) is fixed to S (shaft) by P (synchronization pin).ī1 (boss 1) slides Xst to the right, and the end face hits B2 and pushes B2.Īt that time, C (Countersink) of B1 is right above P. ②Joint constraints with low internal calculation load do not have left / right synchronization function. There may be cases where left-right synchronization failure occurs due to an error due to increased calculation load. ①In the case of contact restraint, calculation load is high and slow. You need a browser that supports the video tag to play videos. △Please check with the play button on the video. (1)Confirmation of rack and pinion operation 2.Problems of current 3D-CAD including examples of operation results of Fusion 360 (based on me10 customization experience) I got a job at a tire manufacturer group company in 1981, and have been engaged in tire manufacturing equipment and tooling design, quality control and sales for 38 years.Īfter introducing 2D-CAD me10 (made by Hewlett Packard) in 1987, I customized it.īased on that experience and the result of operating 3D-CAD Fusion 360 (made by Autodesk), I considered A vision of mechanical 3D-CAD 10 years from now. Top page ■Ideal standard of mechanical 3D-CAD 10 years from now Ideal standard of mechanical 3D-CAD 10 years from now Okanobu Mechanical Engineering and Quality Consultant
